Key numbers for this project
-
HECTARES
-
TONS OF HARVEST
-
CO2 TONS CAPTURED
Hemp field
Mid-season crop growth
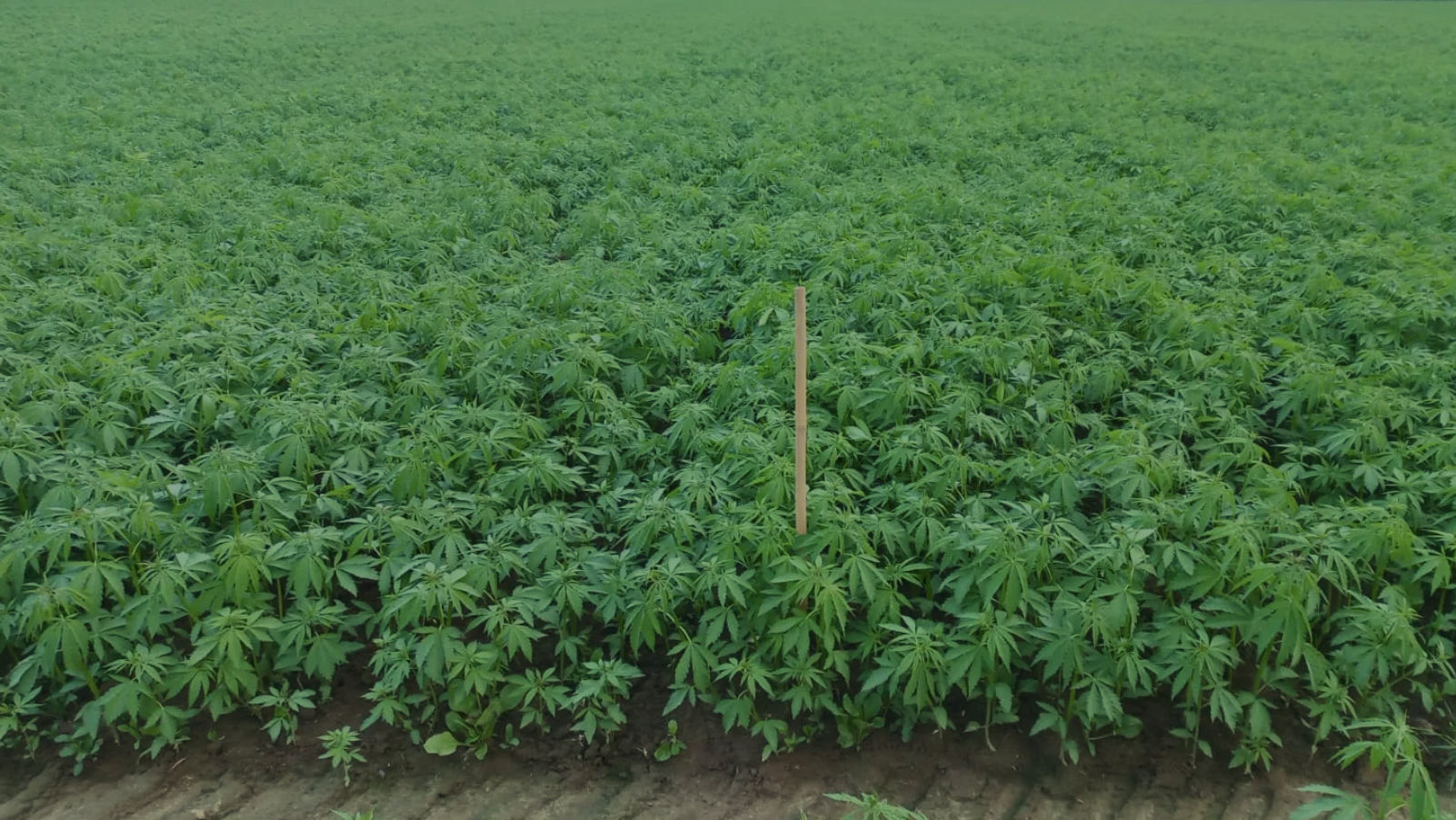
Hemp field
September hemp harvesting
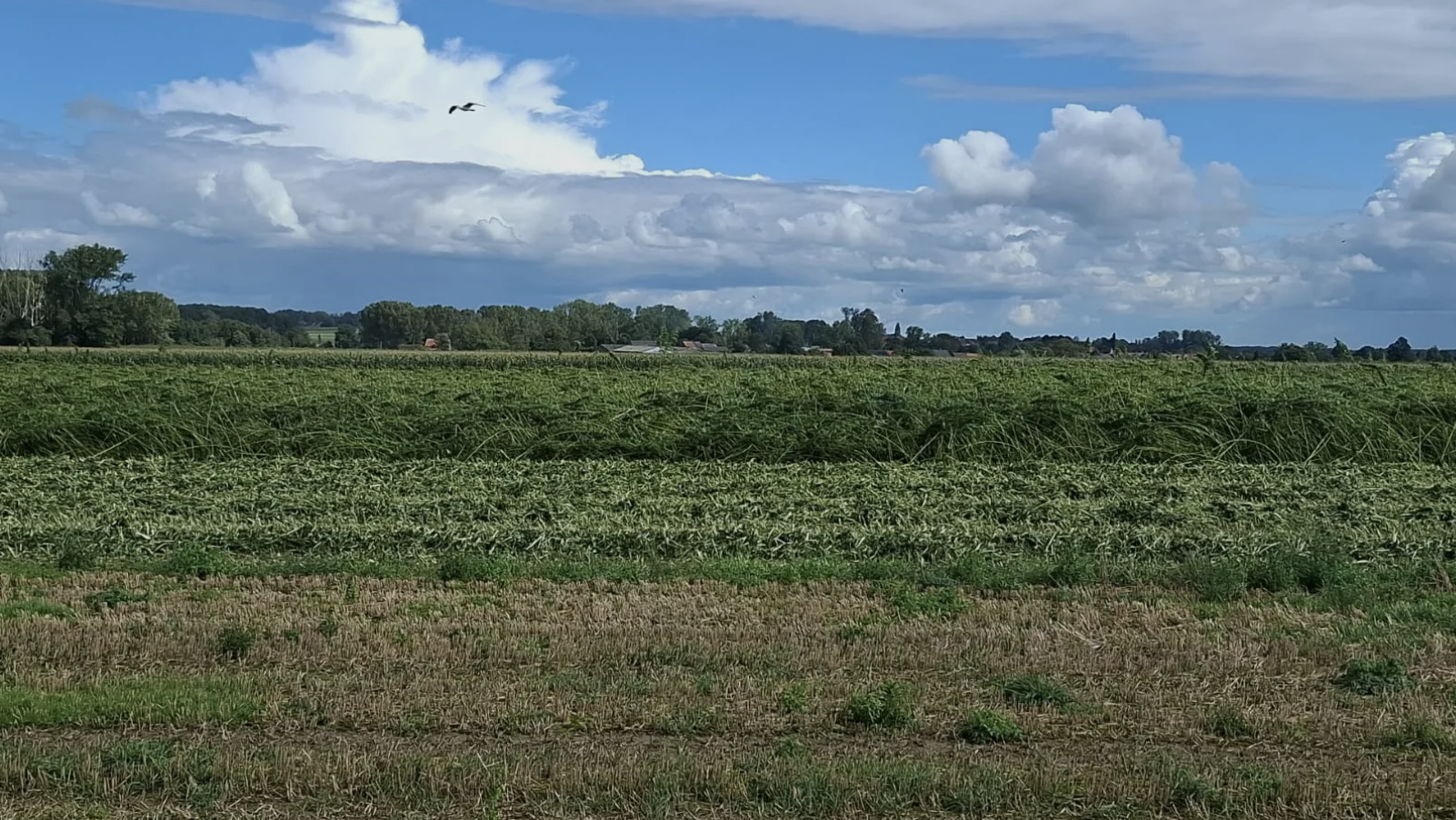
Satellite imagery loop - plot 1
Hemp plants growth curve visible from space
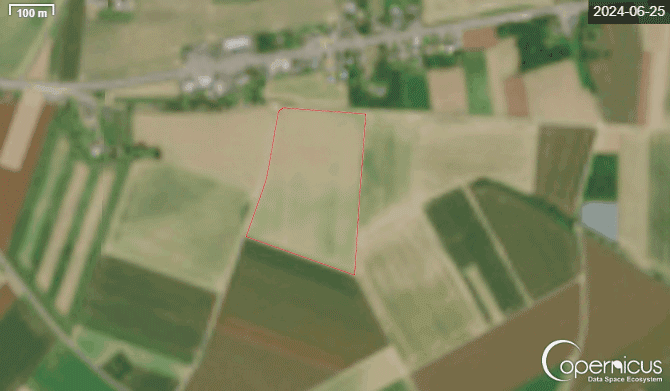
Satellite imagery loop - plot 2
Hemp plants growth curve visible from space
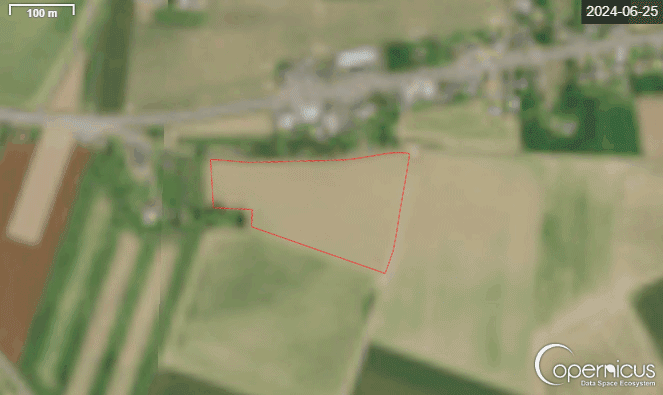
Satellite imagery loop - plot 3
Hemp plants growth curve visible from space
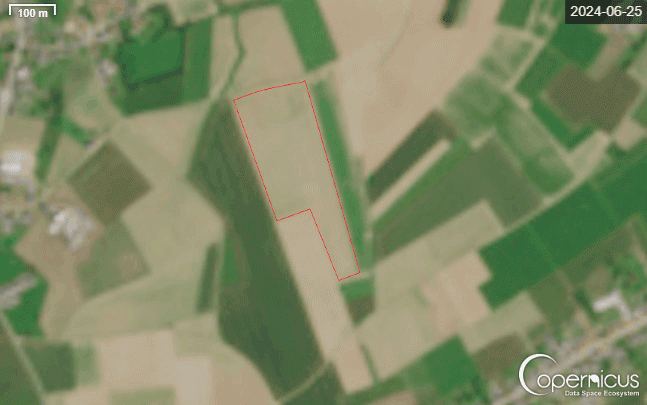
Hemp wood
Circular particle board replacement
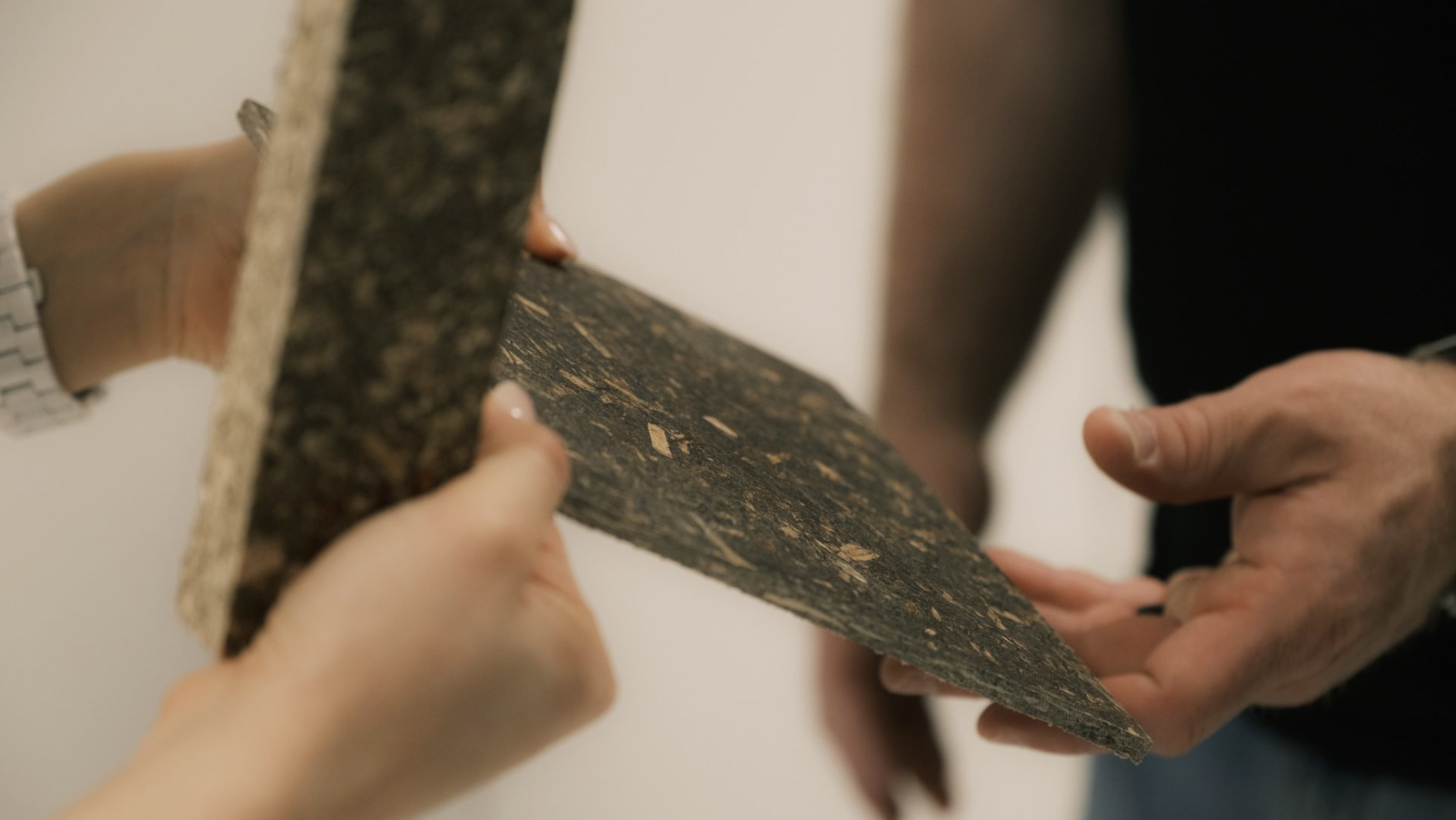
Sandwich panel
Traditional sandwich panel from wood and polyurethane vs bio-based sandwich panel from hemp wood and mycelium
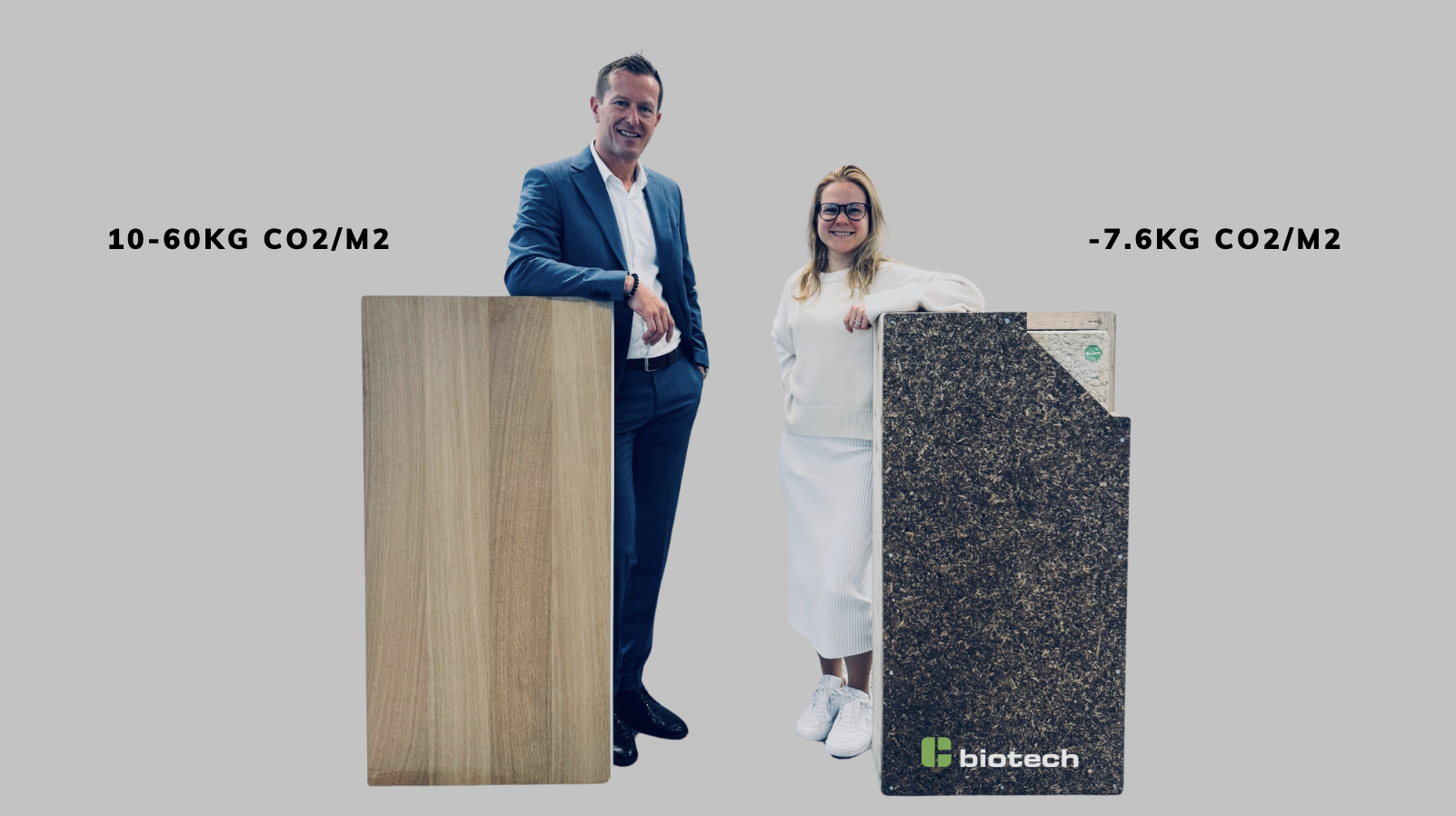
Hemp rotation agriculture: sustainable farming in action
-
2 m
HEMP GROWH IN 3 MONTHS
-
10 CO2 tons
CAPTURED PER HECTARE
Welcome to an innovative agricultural project in Tienen, Belgium. It covers a surface area of 24 hectares. The soil type of this land is 100% loam.
Monitored by Team Hageland, the hemp on this land was sown at the beginning of June 2024 and harvested mid-September 2024.
The farmer grew hemp as a rotation crop. Previous years, the following crop varieties were grown: arboriculture, corn, winter barley, potatoes and sugar beets.
The project showcases the potential of hemp as a rotation crop for sustainable farming practices to increase soil biodiversity, boost harvest yield and produce carbon-negative materials in the process.
Construction materials: hemp wood and sandwich panel
-
-7,60 kg CO2
REMOVED PER M2 OF MATERIAL
-
10 %
BETTER HEAT CAPACITY
Harvested hemp biomass will be transformed into innovative bio-based materials, including hemp wood and sandwich panels. These products are carbon negative, circular and help save up to 500 trees per hectare per year due to fast growing hemp cycle.
Hemp wood boards:
- Composition: 90% hemp shives, 10% biobased pMDI binder
- Production process: hot pressing
- Alternative for particle boards and plywood. Lightweight yet strong, they are ideal for various applications, including flooring, furniture, and interior design.
Sandwich Panel:
- Composition: hemp wood boards combined with mycelium panels, cutting edge bio-based alternative to polyurethane
- Production process: sterilisation of organic matter and growing mycelium within the sandwich panel structure
- Alternative for classic sandwich panels in high-rise buildings and industrial warehouses.
- Life-cycle assessment: the panel is backed by a comprehensive LCA, showcasing a significantly reduced environmental impact throughout its lifecycle, from raw material sourcing to end-of-life disposal. Compared to alternatives that emit 10-60 kg CO2/m2, this sandwich panel sequesters a net 7.6 kg CO2/m². More details here.
Join us in pioneering the future of sustainable construction.
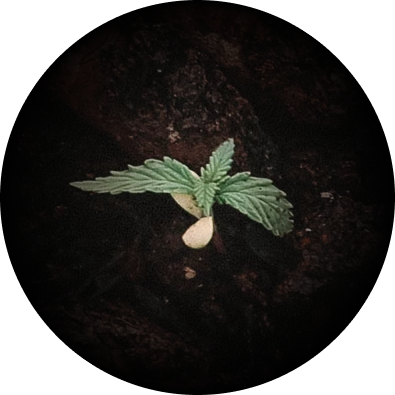
Make your stakeholders proud. Including your mom.
Lead purposeful and profitable business projects with us.
Get in touch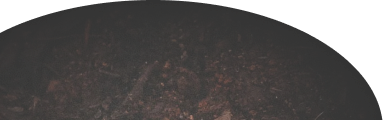